Các nhà nghiên cứu xác nhận cấu trúc tối ưu của vật liệu tổng hợp được tạo ra với sản xuất bồi đắp
Sản xuất bồi đắp đã tạo ra bước phát triển như mong đợi với các máy in 3D sử dụng các polyme để tạo ra một vật thể rắn từ mô hình Thiết kế được hỗ trợ của máy tính. Vật liệu sử dụng là các polyme nguyên chất: phù hợp để tạo khuôn nhanh nhưng không thường được sử dụng để làm vật liệu kết cấu.
Một làn sóng mới của sản xuất bồi đắp là sử dụng vật liệu polyme tổng hợp được ép đùn từ vòi phun giống nhựa epoxy, nhưng gia cố bằng xơ cacbon được cắt ngắn. Các xơ này làm cho vật liệu bền hơn, giống như lõi thép trong vỉa hè xi măng. Vì vậy, sản phẩm trở nên cứng hơn và bền hơn hơn so với vật liệu nguyên chất.
Câu hỏi mà một nghiên cứu gần đây của Đại học Illinois tại Urbana-Champaign đặt ra để trả lời cho những lo ngại về cấu hình hoặc kiểu xơ cacbon trong các lớp nhựa ép đùn sẽ dẫn đến vật liệu cứng nhất.Giáo sư John Lambros, Willett thuộc Khoa Kỹ thuật hàng không vũ trụ và là giám đốc Phòng đánh giá và thử nghiệm vật liệu tiên tiến tại Đại học Illinois tại Urbana-Champaign đã được một nhóm nghiên cứu sản xuất bồi đắp tại Phòng thí nghiệm quốc gia Lawrence Livermore tiếp cận để kiểm tra các thành phần của vật liệu tổng hợp mà họ đã tạo ra bằng kỹ thuật viết mực trực tiếp.
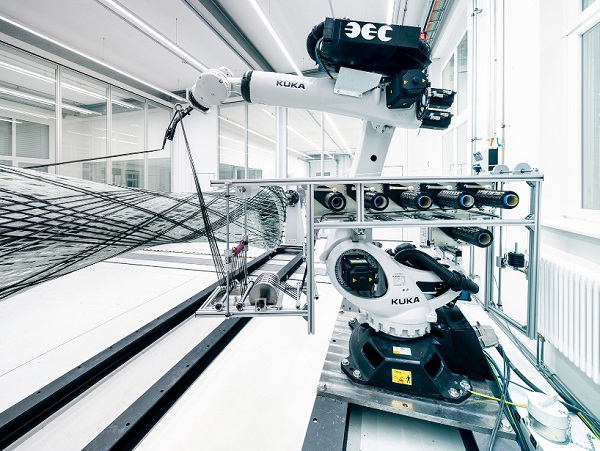
Theo Giáo sư Lambros: “Các xơ cacbon nhỏ với đường kính khoảng bảy micron và dài 500 microns được nhìn thấy dễ dàng hơn dưới kính hiển vi nhưng có thể nhìn thấy dạng kết bó bằng mắt thường. Các xơ chủ yếu được xếp định hướng trong nhựa ép đùn, giống như một loại keo cố định vị trí các xơ. Nhóm nghiên cứu Lawrence Hepmore cung cấp các bộ phận được tạo ra bằng một vài cấu hình khác nhau và một mẫu đối chứng được tạo ra mà không có bất kỳ xơ nào được đưa vào để cố định. Một trong những bộ phận đã được tối ưu hóa về mặt lý thuyết cho độ cứng tối đa, nhưng nhóm nghiên cứu muốn xác thực thử nghiệm tối ưu hóa quá trình”.
Giáo sư Lambros cho biết: Trong khi chờ đợi các mẫu composite sản xuất bồi đắp thực tế, ông và sinh viên của ông đã tạo ra các mẫu “hình nộm” từ thủy tinh hữu cơ để bắt đầu thử nghiệm các hình nộm này. Trong trường hợp này, hình dạng đang được thử nghiệm là khớp nối giữa một tấm nhỏ hình bầu dục với hai lỗ được sử dụng để kết nối hai bề mặt khác. Đối với mỗi hình dạng mẫu khác nhau, phòng thí nghiệm của Lambros phải tạo ra một vật tải duy nhất để kiểm tra.
Ông Lambros cho hay: “Chúng tôi tạo ra giá đỡ, tay cầm, các vật dụng khác và sơn chúng sao cho các máy ảnh sẽ ghi lại các phép thử, v.v. Khi chúng tôi có được các mẫu thật, chúng không có hình dạng giống hệt nhau. Độ dày của những mẫu này hơi khác so với mẫu thủy tinh hữu cơ của chúng tôi, vì vậy chúng tôi đã tạo ra các miếng đệm mới để sử dụng trong khâu cuối. Về khía cạnh cơ học, chúng tôi phải rất thận trọng. Việc sử dụng chính xác là cần thiết để đảm bảo rằng mọi chứng nhận cuối cùng của các bộ phận được sản xuất bồi đắp đều được thực hiện đúng “.
Giáo sư Lambros nói: “Chúng tôi đã tạo ra một hệ thống thí nghiệm để xác nhận mô hình tối ưu của vật liệu composite cốt xơ ngắn. Khi máy hoạt động làm căng các tấm khớp, chúng tôi đã sử dụng kỹ thuật tương quan hình ảnh kỹ thuật số (digital image correlation) để đo trường dịch chuyển trên bề mặt của mỗi mẫu bằng cách theo dõi chuyển động của giá trị cường độ điểm ảnh của một loạt các hình ảnh kỹ thuật số khi mẫu biến dạng. Một đốm ảnh ngẫu nhiên được áp dụng cho bề mặt mẫu và dùng để xác định các tập hợp con của hình ảnh kỹ thuật số theo cách độc đáo để chúng có thể được theo dõi trong suốt quá trình biến dạng”.
Nhóm nghiên cứu đã thử nghiệm trên một mẫu đối chứng và bốn mẫu cấu hình khác nhau, bao gồm một mẫu được cho là độ cứng tối ưu, tức là mẫu có xơ lượn sóng chứ không phải là mẫu có xơ được định hướng theo chiều ngang hoặc dọc.Giáo sư Lambros cho biết: “Mỗi mẫu khớp nối có 12 lớp trong một chồng. Mẫu tối ưu hóa có các đường cong lắng đọng và giữa chúng có khoảng cách. Theo dự đoán của nhóm Livermore, các khoảng trống đó là ý đồ thiết kế bởi vì không cần nhiều vật liệu hơn mức này để tạo ra độ cứng tối ưu. Đó là những gì chúng tôi đã thử nghiệm. Chúng tôi đã bỏ qua các tải trọng qua các lỗ, sau đó kéo từng mẫu đến điểm đứt, ghi lại lượng tải và khoảng cách dịch chuyển”. Cấu hình tối ưu mà họ dự đoán thực sự là tối ưu. Mẫu đối chứng ít tối ưu nhất vì không có cốt xơ.Theo ông Lambros, tiền đề phân tích chỉ ra đây là mẫu tối ưu toàn cầu – có nghĩa đây làmẫu hoàn toàn tốt nhất có thể được chế tạo đạt được độ cứng – không có mẫu nào được chếtạo tốt hơn.Ông Lambros nói: “Mặc dù chúng tôi chỉ thử nghiệm bốn cấu hình nhưng có vẻ như cấu hình được tối ưu hóa có thể được sử dụng một cách tốt nhất vì trong thực tế các cấu hình này thường được sử dụng trong thiết kế. Chẳng hạn như sắp xếp 0°-90° hoặc ± 45° khó thực hiện hơn hoặc ít cứng hơn so với sử dụng cấu hình này. Điều thú vị mà chúng tôi tìm thấy là mẫu được tối ưu hóa là cứng nhất cũng là bền nhất bởi vì khi khi kéo đứt mẫu có lực kéo đứt lớn nhất. Điều này hơi bất ngờ bởi vì mẫu đã không được tối ưu hóa cho tính năng này. Trên thực tế, mẫu được tối ưu hóa cũng nhẹ hơn một chút so với các mẫu khác, vì vậy nếu nhìn vào tải trọng cụ thể, tổn thất tải trọng trên mỗi đơn vị trọng lượng sẽ cao hơn rất nhiều. Mẫu này bền hơn những mẫu khác. Và đó là lý do chúng tôi sẽ tiếp tục nghiên cứu”
Ông Lambros cho biết có thể có nhiều thử nghiệm được thực hiện sắp tới, nhưng hiện tại, nhóm nghiên cứu của ông đã giải thích thành công rằng họ có thể tạo ra vật liệu composite bồi đắp tối ưu.
https://www.sciencedaily.com/releases/2019/06/190627171552.htm?fbclid=IwAR3FR16yL36iMJeLTE7jl1xoaXaQMZmitwIg7wpWH9qhOGYC7_AyHDipG-k
Người dịch: Võ Thị Lan Hương